Discovering the Applications of Plastic Injection Molding Throughout Industries
Plastic shot molding stands as a cornerstone of contemporary manufacturing, using amazing adaptability across diverse fields such as auto, consumer products, healthcare, and electronic devices. Comprehending just how these improvements affect the landscape of production can disclose much concerning future fads and techniques.
Automotive Industry Innovations
Transforming the automobile landscape, plastic injection molding has emerged as a crucial modern technology in the production of innovative vehicle elements. This manufacturing procedure permits the development of lightweight components and complex geometries, dramatically adding to automobile performance and performance.
In modern-day auto style, plastic shot molding helps with the production of parts such as bumpers, control panels, and indoor trim pieces. These elements not only enhance aesthetic charm but likewise boost safety and security and capability. The capacity to mold complex styles enables the combination of advanced features like airbag systems and digital user interfaces straight into the structural parts.
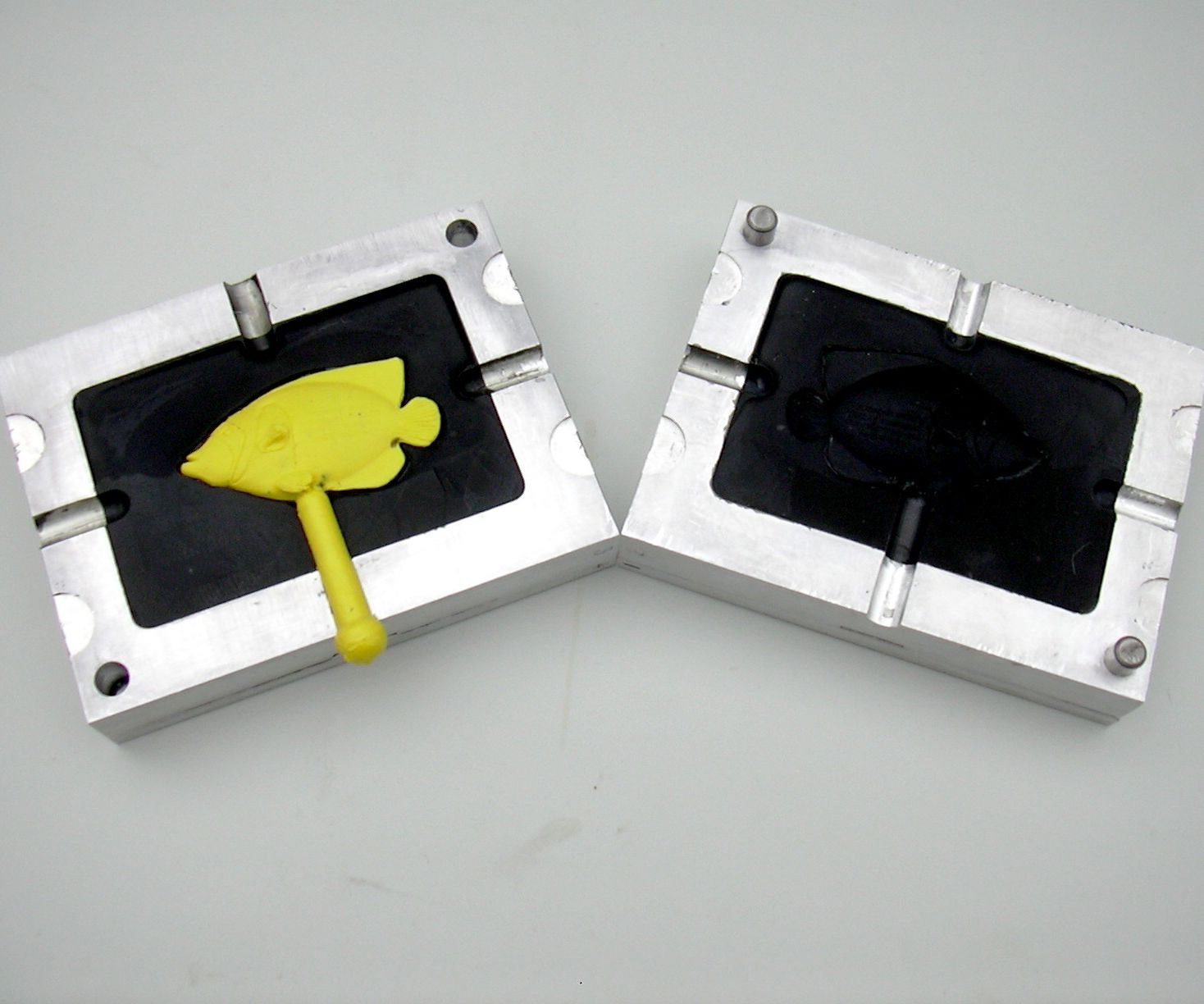
As the vehicle market continues to embrace electrical and independent technologies, the function of plastic injection molding will come to be increasingly important. Its adaptability and efficiency position it as a keystone modern technology for future advancements in automobile design and production, driving improvements toward a more sustainable vehicle community.
Durable Goods Production
The impact of plastic shot molding extends past the automobile sector, substantially influencing consumer products manufacturing. This functional technique allows the production of a wide variety of items, varying from family products to complex electronic elements. The capacity to create intricate forms and designs with high precision enables manufacturers to meet customer demands for both capability and appearances.
Among the primary benefits of plastic shot molding in durable goods is its efficiency. The process enables high-volume production, lowering manufacturing prices and preparation. This performance is important in a market defined by quickly altering customer preferences and patterns.

Eventually, plastic injection molding acts as a cornerstone in durable goods making, allowing the creation of diverse, high-quality items that accommodate evolving market demands while optimizing functional performance. This versatility guarantees its ongoing importance in the affordable landscape of customer items.
Health Care Applications
In the medical care industry, plastic injection molding plays a crucial duty in the manufacturing of a wide variety of medical gadgets and components. This production strategy enables the development of complicated and precise forms needed for various applications, from medical tools to diagnostic tools.

Furthermore, plastic injection molding permits the assimilation of features such as texturing and facility geometries, which can boost the capability and customer experience of medical tools. The process likewise supports fast prototyping and short preparations, allowing makers to react promptly to market needs and technological innovations.
Electronics Manufacturing Methods
As markets significantly count on innovative production processes, plastic injection molding has also discovered substantial applications within electronic devices manufacturing. This strategy permits for the effective creation of detailed elements that are crucial for modern-day digital gadgets. From smartphone cases to circuit card, the accuracy and convenience of shot molding assist in the production of high-quality parts that meet extensive visit this website market standards.
Among the vital benefits of plastic injection molding in electronic devices is its capability to create complex geometries that would certainly be see here now challenging to achieve with conventional production methods. The quick cycle times connected with the procedure also enhance manufacturing performance, enabling suppliers to react swiftly to market demands.
Additionally, the use of specialized thermoplastics can enhance the efficiency of digital elements. Products such as polycarbonate and ABS use high sturdiness and excellent electric insulation, making them excellent for applications ranging from adapters to housing units.
Furthermore, shot molding sustains the combination of numerous functions into single parts, lowering setting up time and expenses. As modern technology proceeds to advance, the role of plastic shot molding in electronics production is likely to broaden, driving advancement and improving item performance throughout the sector.
Sustainability in Shot Molding
Sustainably incorporating methods in injection molding significantly forms the future of manufacturing, dealing with growing ecological worries. As sectors pursue eco-friendliness, the injection molding process adapts by implementing lasting materials and energy-efficient modern technologies. Recycled and naturally degradable plastics are acquiring traction, lowering dependence on nonrenewable fuel sources and lessening waste.
In addition, improvements hop over to here in machinery and strategies aim to reduced energy usage throughout manufacturing. For circumstances, electrical shot molding devices are coming to be much more common, providing significant decreases in energy use compared to standard hydraulic systems. These machines not only preserve power yet likewise boost precision and minimize cycle times, resulting in reduced functional costs.
Additionally, firms are adopting closed-loop systems to handle waste effectively. By reusing scrap product produced throughout the manufacturing process, they can lessen environmental impact and promote source effectiveness (Plastic Injection Molding). Implementing lasting techniques in shot molding not only fulfills regulatory requirements however also deals with the increasing customer demand for eco liable products
Conclusion
In conclusion, plastic injection molding serves as an important manufacturing process across numerous sectors, including automotive, customer goods, healthcare, and electronics. Hence, plastic injection molding remains crucial for meeting the vibrant needs of contemporary markets while advertising lasting production methods.
Plastic injection molding stands as a keystone of modern-day production, offering impressive flexibility throughout diverse industries such as vehicle, consumer items, healthcare, and electronic devices.In contemporary automobile design, plastic shot molding assists in the production of elements such as bumpers, dashboards, and indoor trim pieces.As markets progressively rely on innovative manufacturing processes, plastic injection molding has actually additionally located significant applications within electronic devices manufacturing.In conclusion, plastic injection molding offers as an important manufacturing process throughout various sectors, including automobile, consumer products, healthcare, and electronics. Therefore, plastic shot molding remains essential for meeting the dynamic demands of modern-day markets while promoting lasting manufacturing techniques.